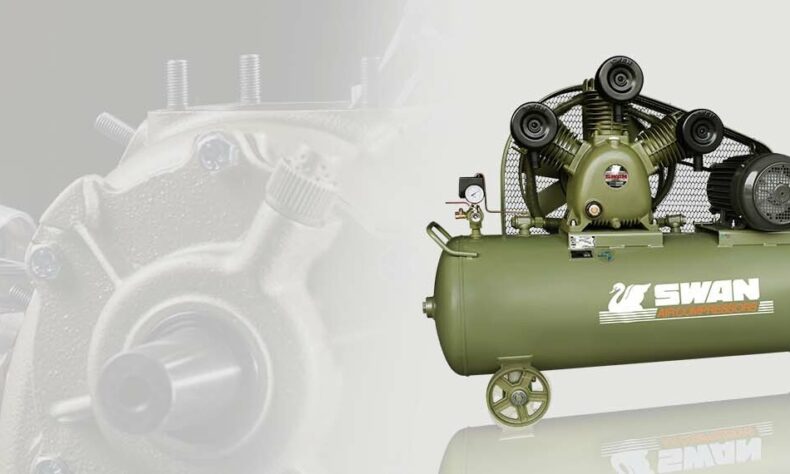
Any firm that uses air compressors needs to keep them operating smoothly and effectively. Additionally, since it will be more effective and last longer than one that has not been properly maintained, a well-kept air compressor will save you money over time. That is why it is crucial to have an air compressor maintenance checklist.
You can see issues before they worsen and take action to stop them from happening altogether by using a thorough air compressor maintenance checklist. This tutorial will provide you with a general overview of the items that should be on your air compressor maintenance checklist, explain how to make one, and offer some advice for keeping your air compressors operating at their best.
What is Maintenance on an Air Compressor?
The act of doing regular and preventative maintenance on air compressors to make sure they are operating effectively and safely is known as air compressor maintenance. This entails testing the air compressor for problems, lubricating moving components, cleaning air filter elements, checking air pressure, and more.
Why Regular Air Compressor Maintenance is Important?
Regular preventative maintenance is necessary for air compressors to support and enable effective energy delivery. Vehicle air compressor suppliers regularly do maintenance to prevent expensive repairs, reduced performance, and even dangerous situations. However, regular maintenance of air compressors ensures the following:
Ensure air compressor effectiveness
Air compressors need to be properly maintained to operate at their highest efficiency and production. Regular air compressor maintenance makes sure they are operating as effectively and efficiently as possible, which can ultimately save you money.
Lower Your Chances of an Air Compressor Failure
For air compressors to operate effectively and dependably, regular maintenance is necessary. Additionally, by assisting in the early detection of possible difficulties before they develop into serious ones, it lowers the likelihood of air compressor failure.
Maintain Safety
Depending on the sort of air compressor you have, you might need to do air compressor maintenance to make sure it’s safe to use. The likelihood of accidents can be decreased by identifying potential safety issues and taking the necessary precautions with regular air compressor maintenance.
Verify Compliance
Air compressor maintenance is necessary to guarantee the safe and effective operation of these devices, according to international standards like ISO 45001 and the United States Occupational Safety and Health Administration. For compliance with these requirements, regular air compressor maintenance is required. At the same time, it lowers the possibility of air compressor failure and aids in the most effective operation of air compressors.
What exactly is a checklist for air compressor maintenance?
The tasks that need to be finished during air compressor repair are listed on a checklist. Users and service providers of air compressors can efficiently accomplish the necessary air compressor maintenance tasks by using a checklist.
The necessary preventative maintenance activities for air compressors should be included on the maintenance checklist, along with step-by-step instructions on how to carry out each task. Along with operation instructions, a reference manual for air compressor parts should be included.
Tips and Guide
Regular compressed air system maintenance helps to prevent future problems, ultimately saving you or your company time and money. Additionally, it’s crucial to be proactive and deal with problems before they arise. When you can contribute to its prevention, why deal with the strain of a problem?
Replace your air filter
It should come as no surprise that one of the most crucial components of your compressed air system is air, making it crucial to maintain a clean air intake. Your air compressor filter functions as a doorway between filthy and clean by guarding against dust, aerosols, and oil vapors, much like our nostrils filter the air entering our dust and debris are removed from the lungs and air conditioner filters..
Additionally, a dirty air filter means that your compressor will have to work harder (and consume more energy) to function effectively and get the results you want. This results in greater electrical expenses, which, if you don’t maintain your system under control, can increase quickly over time.
Look for Leaks and Inspect the Hoses
Air moves quickly and at extremely high pressure from one location to another in compressed air systems. Even though leaks are occasionally unavoidable, you can take steps to significantly lower their frequency. If system leaks go undetected, your compressor must work harder to make up for it, which raises your electricity expenses.
Examine the joints, connectors, and hoses in your system carefully to look for leaks. Hoses can occasionally corrode or split as a result of poor maintenance. Avoid bending or kinking hoses as this might alter pressure and impede flow.
Alter the oil filter
Your system’s oil filter is essential in keeping dirt, sand, rusty bits, and other undesirable debris out of your compressor, much like air filters remove undesired particles. However, oil free compressor manufacturers consider the element that contributes to unneeded electricity costs as a clogged filter. It can lead to a compressed air system that is overworked. Additionally, it might cause unneeded heat.
You should try to change your oil filter at regular intervals between 2,000 and 4,000 hours. Mainly, depending on the brand, size, and type of compressor you have. For the precise number, consult the manual or the manufacturer.
Check the Level of the Lubricant and Oil
If your vehicle urgently required an oil change, would you still drive it? Oil and lubricants in your compressor system keep everything functioning smoothly and effectively. Low oil levels might damage your system and result in expensive repairs or replacements.
How long oil in your air system lasts is significantly influences heat. “Oil life” relates to how long oil remains in your body. If you discover that the oil life of your compressor is decreasing or is much lower than the industry norm, there might be an issue with the heat load or another factor at play.
A Separator Element Replacement
The oil separator, to put it simply, separates oil from air. Because compressed air must leave the compressor without any oil, the condition of the oil separator is crucial. This component prevents the overuse of oil by allowing it to cycle back into the system.
Maintaining the oil separator in good condition is crucial to preserving the overall health of your system. Since without it, your energy expenses will certainly increase.